Hoosier Feeder Company understands the value of production time and the detriment down-time can cause. That is why before your feeding system leaves our facility, we ask ourselves, “How can we make our system’s integration as seamless as possible?”. That question is answered in the form of
checklists and tests prior to shipment. We cannot account for unknown circumstances once the feeder leaves our facility so we make sure that our system is rock solid so your effort can be directed elsewhere.
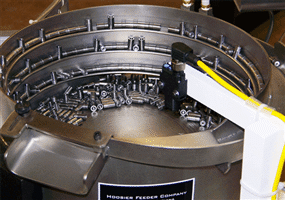
In addition to the frequent checks and tests throughout the build process we systematically verify feeder system performance:
We first address the most important aspect of a feeder system: functionality. We begin static tests by once again verifying that the part orientation is what was required. Then, in the case of centrifugal jobs, we scour the numerous bolts throughout the system to check for tightness ensuring all tooling, brackets, and mechanisms are held solidly in place. For vibratory feeders we check every weld for consistency and cracks along with each tooling section for adjustability and effectiveness as well as polished and ground seams for
pharmaceutical or
food/beverage applications.

Next begin our dynamic tests. Each feeder undergoes a minimum 2 hour, uninterrupted run test. For centrifugal feeders we take care to observe noise and vibration throughout the machine as this is a sign of component interference.
Vibratory feeders are checked for tuning and balancing to ensure there are no “dead” spots on the bowl verifying it will run predictably and jam-free. During this test we check feed rates every minute for 10 consecutive minutes, using a safety margin of 10-20% (higher than required rate) to ensure we will meet or exceed the part feed rate you need. Builders are careful to fine-tune air settings, bowl amplitudes, control settings, and any other adjustments to further solidify feeder functionality. If we encounter any major issues, we correct them and begin the testing again.
One important group of tests are the “fit and finish” verifications. We re-check dimensions, verify that all coatings and finishes are up to our standards, and make sure that all edges are smooth and deburred. We make sure your system will look good and be safe in your facility. To conclude our project send-off, we make sure to thoroughly clean and wipe down all feeder systems before we ship them to be integrated into your production line. We at Hoosier Feeder Company believe the finishing details are among the most important, which is why we happily devote as much time and effort as is necessary to deliver the best possible feeding system.
October 24, 2017